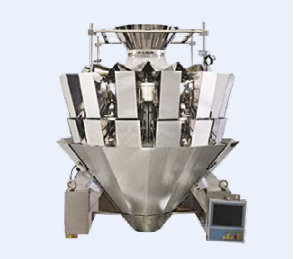
1. Product Characteristics and Handling Requirements
The physical attributes of your products play a significant role in determining the suitable feeding mechanism. Items that are small, irregularly shaped, or sensitive require feeding devices designed to handle them gently and accurately. Consider feeding systems equipped with adjustable grippers, conveyors, or vibratory feeders that cater to the specific handling needs of your products.
2. Production Speed and Volume
The speed and volume of your production line are crucial in determining the capacity and efficiency of the feeding device. High-speed feeders are essential for large-scale operations to maintain productivity, while slower, more precise feeders might be better suited for delicate or low-volume products. Assess your current and projected production needs to ensure the feeding device can keep pace.
3. Integration with Existing Packaging Lines
Ensuring seamless integration with your existing packaging machinery is vital. Look for feeding devices that are compatible with your packaging system's interface, control systems, and physical layout. Consider consulting with equipment suppliers or integrators to ensure compatibility and smooth operation.
4. Automation and Control Features
Automation and control features can greatly enhance the functionality of feeding devices. Look for systems that incorporate sensors, adjustable controls, and feedback mechanisms to maintain accuracy and consistency. Automated feeding devices can also reduce labor costs and improve overall efficiency.
5. Durability and Maintenance Requirements
The durability and ease of maintenance of a feeding device are critical factors. Opt for robust, high-quality materials that can withstand the rigors of continuous use. Additionally, consider the availability of spare parts, ease of cleaning, and the manufacturer's support for maintenance and repairs.
6. Cost-Benefit Analysis
Cost is an important consideration, but it should be balanced against the long-term benefits. Evaluate the total cost of ownership, including the initial purchase price, maintenance costs, potential downtime, and product loss. Investing in a reliable, durable feeding device can yield significant savings and improve overall production efficiency.